FutureCar Challenge
Background
FutureCar Challenge, conducted annually between 1995 and 1999, challenged North American universities to design and apply advanced technologies to mid-sized sedans. Parallel to the goals of the Partnership for a New Generation of Vehicles (PNGV), the FutureCar Advanced Vehicle Technology Competition (AVTC) series utilized advanced technologies and hybrid electric vehicle powertrains to achieve 80 miles per gallon, while offering the same comfort, safety, and affordability that consumers expected from conventional vehicles.
Sponsored by the U.S. Department of Energy, the U.S. Council for Automotive Research (USCAR), PNGV, and other North American automotive suppliers, the competition challenged university students to reengineer a Dodge Intrepid, Ford Taurus, or a Chevrolet Lumina. A prototype Mercury Sable was added in to the program for the 1997-1999 years.
Fuel used by the teams included reformulated gasoline, diesel and fischer-trophsch diesel, ethanol, compressed natural gas, liquid petroleum gas, hydrogen, dimethyl ether, and electricity. A wide range of events were held to test the vehicles’ performance and the teams’ ability to communicate their design choices and rationale. Performance improved over time with better batteries, control strategies, and experience. During the later years of the program, two universities were able to experiment with fuel cell stacks and had to adapt the technology to their competition vehicle.
In 1995-1996, 12 university teams competed in a series of dynamic and static events at the Ford Proving Grounds in Dearborn, Michigan. Emissions and fuel economy testing took place at the U.S. Environmental Protection Agency (EPA) National Vehicle and Fuel Laboratory in Ann Arbor, Michigan. The teams then had to embark on a road rally throughout the Detroit metropolitan area.
In 1996-1997, those same 12 teams switched gears and tested their vehicles at General Motors’ Technical Center in Warren, Michigan, followed by emissions and fuel economy testing at U.S. EPA. The teams then participated in a more aggressive over-the-road endurance event, which took place from Warren to Washington, D.C.
During the 1997-1998 program, 13 universities competed in the FutureCar Challenge program. The year-end competition took place in June 1998, which began with technical evaluations at Oakland Community College in Auburn Hills, Michigan. Industry and government engineers measured a variety of vehicle attributes, including range, acceleration, driveability, exhaust emissions, and fuel efficiency. Once again, vehicle emissions testing was held at U.S. EPA and the finale events were held at the Detroit Grand Prix, Chrysler Technology Center, and Greenfield Village.
For the fourth and final year of FutureCar, teams began their technical dynamic and static events again at Oakland Community College with emissions testing at U.S. EPA. However, teams were challenged with an over-the-road endurance test as vehicles were driven in a road rally from Michigan to Washington, D.C. for the finale awards ceremony. Teams made a few pit stops along the way, including stops at West Virginia University in Morgantown, West Virginia and the University of Maryland in College Park, Maryland.
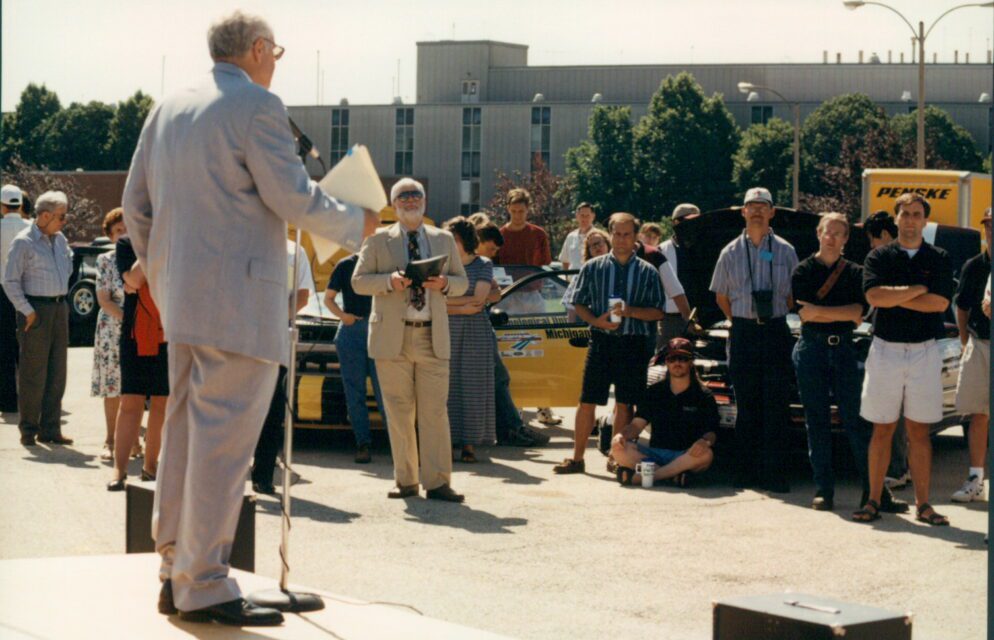
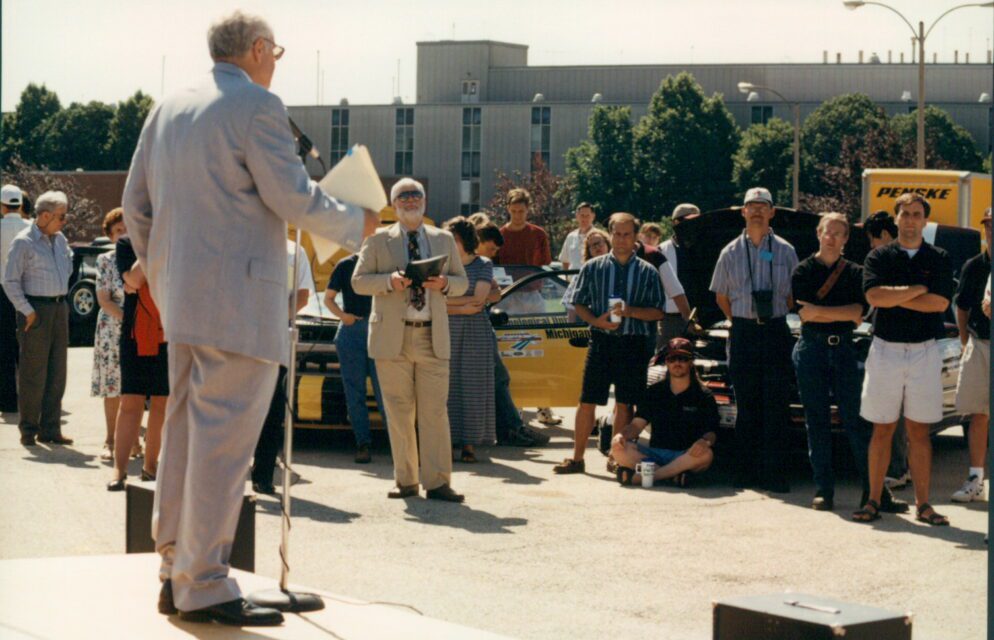
FutureCar
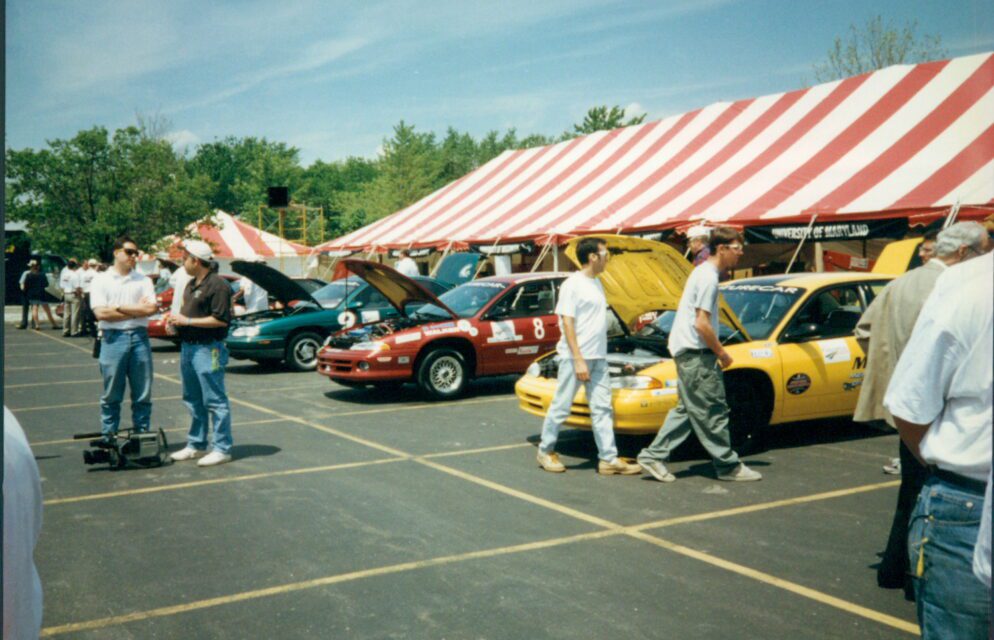
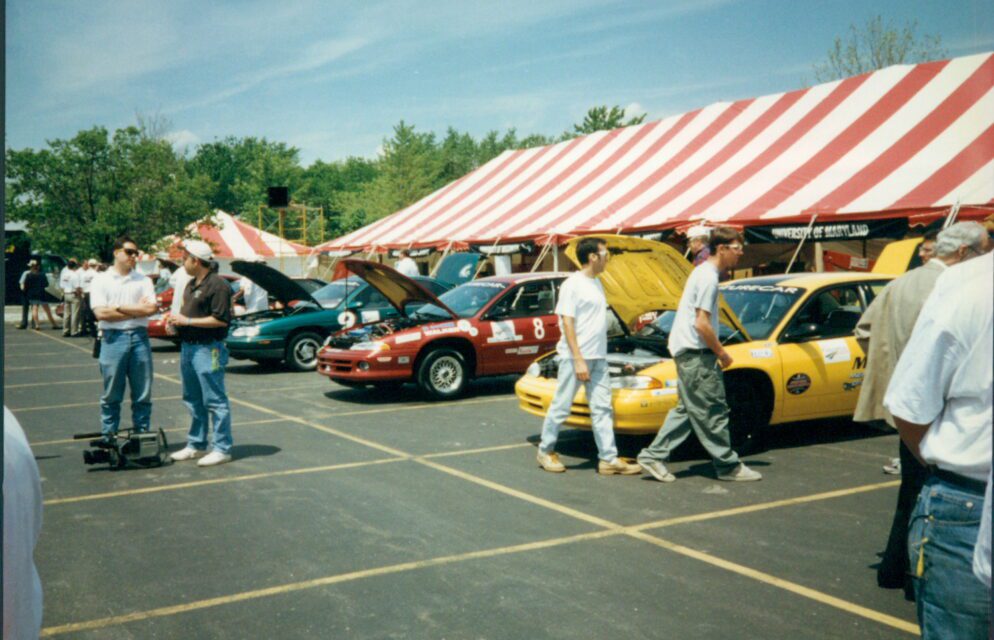
FutureCar
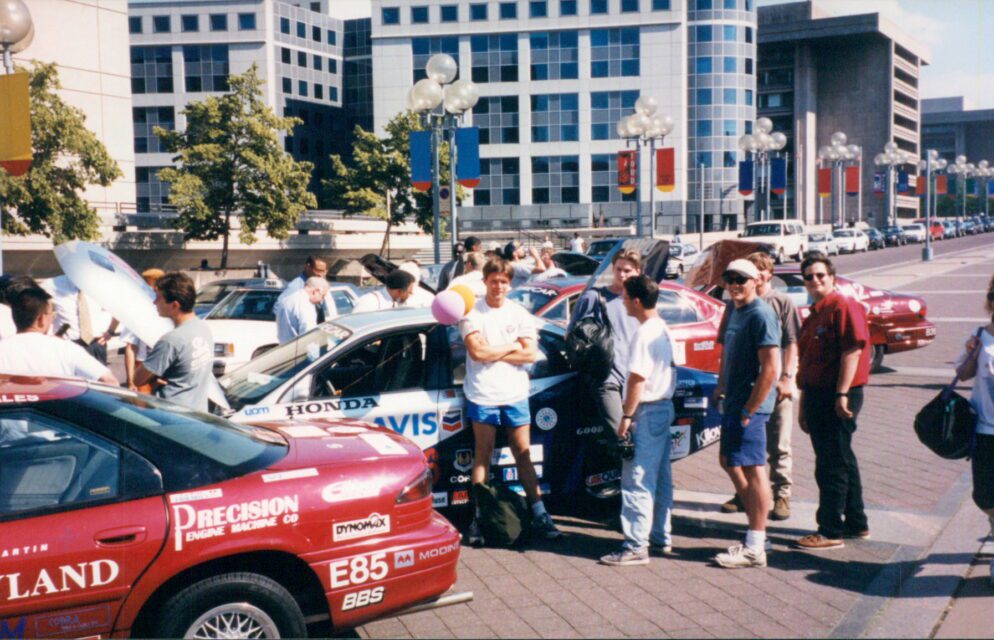
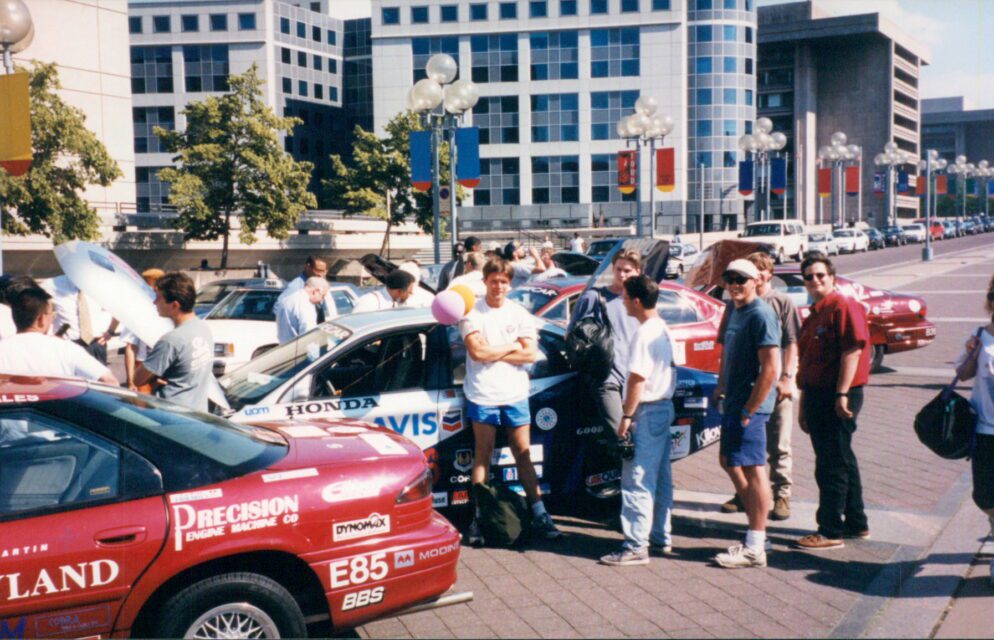
FutureCar
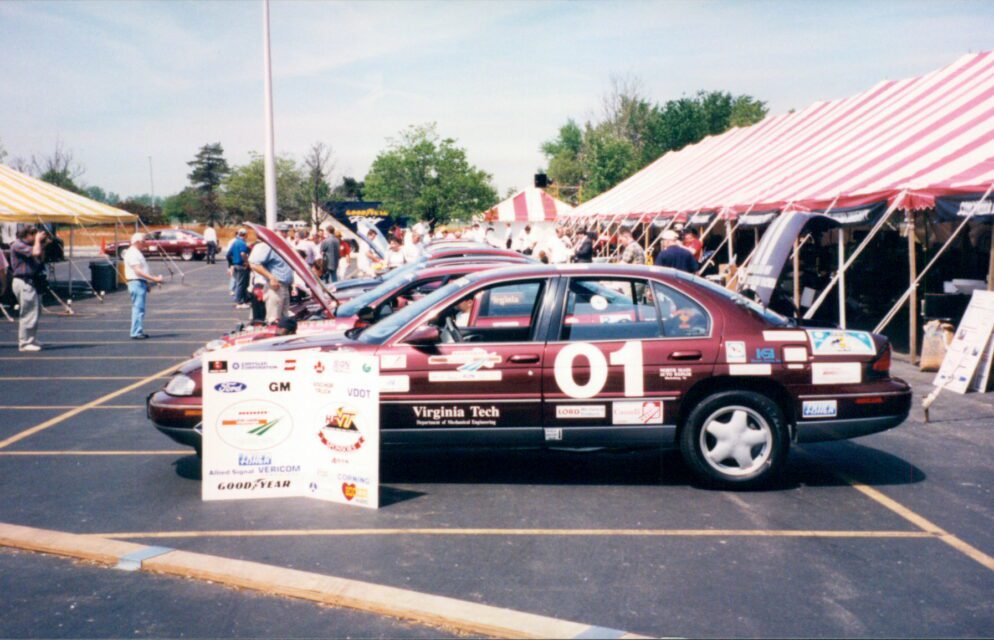
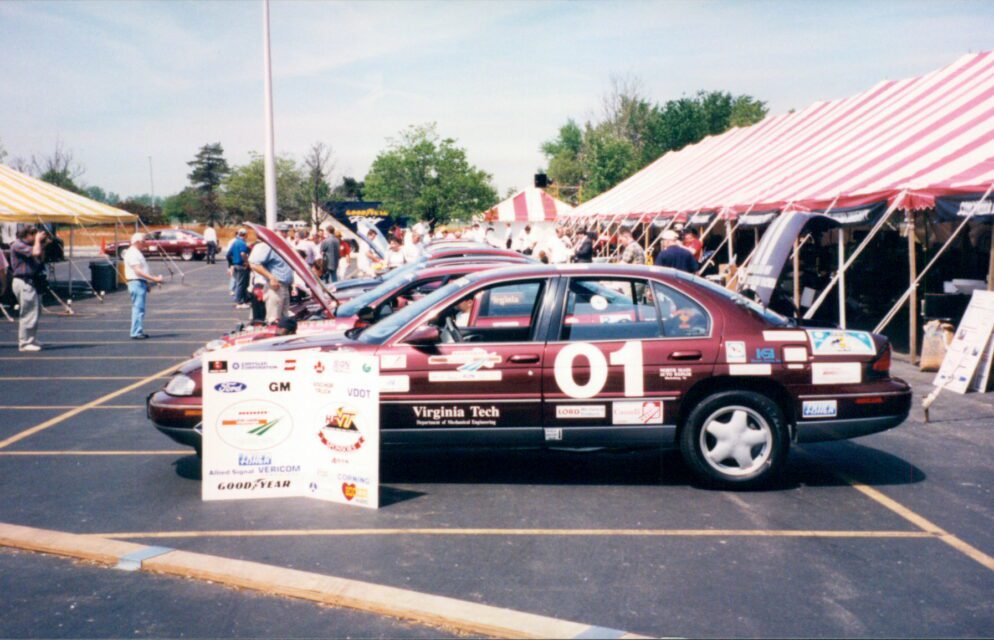
FutureCar
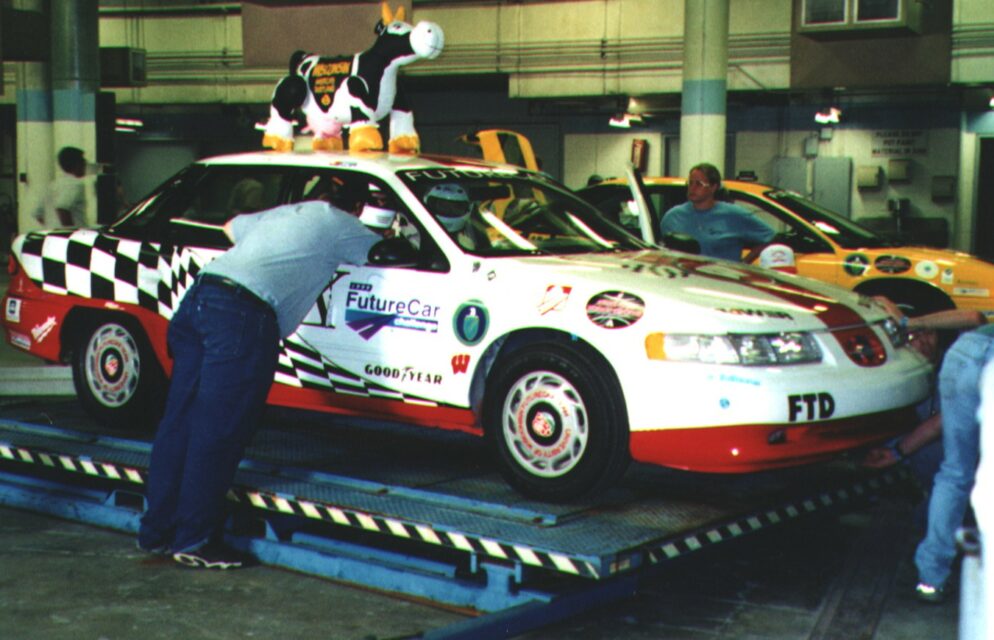
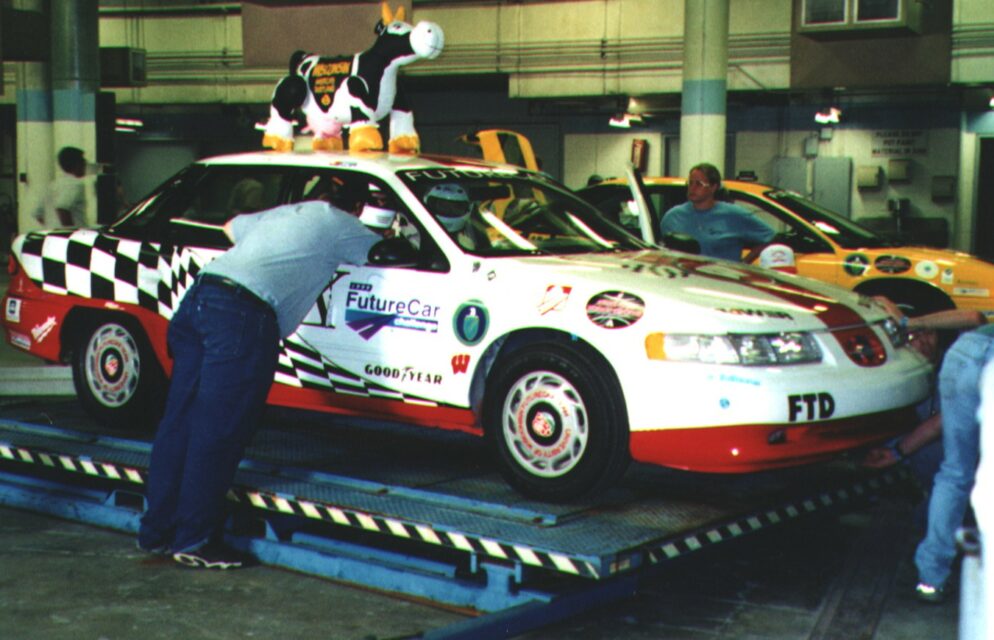
FutureCar
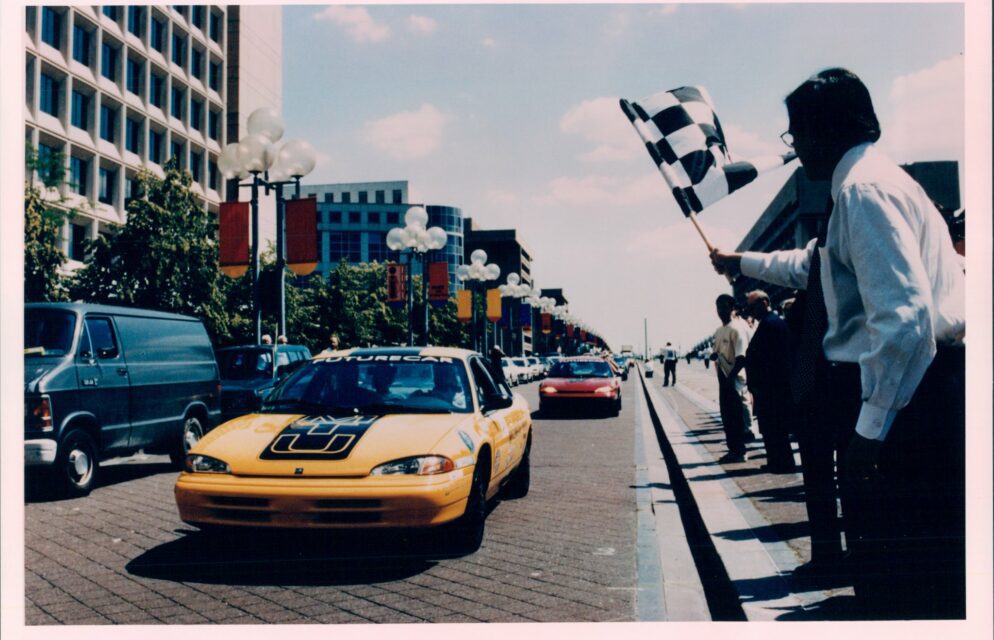
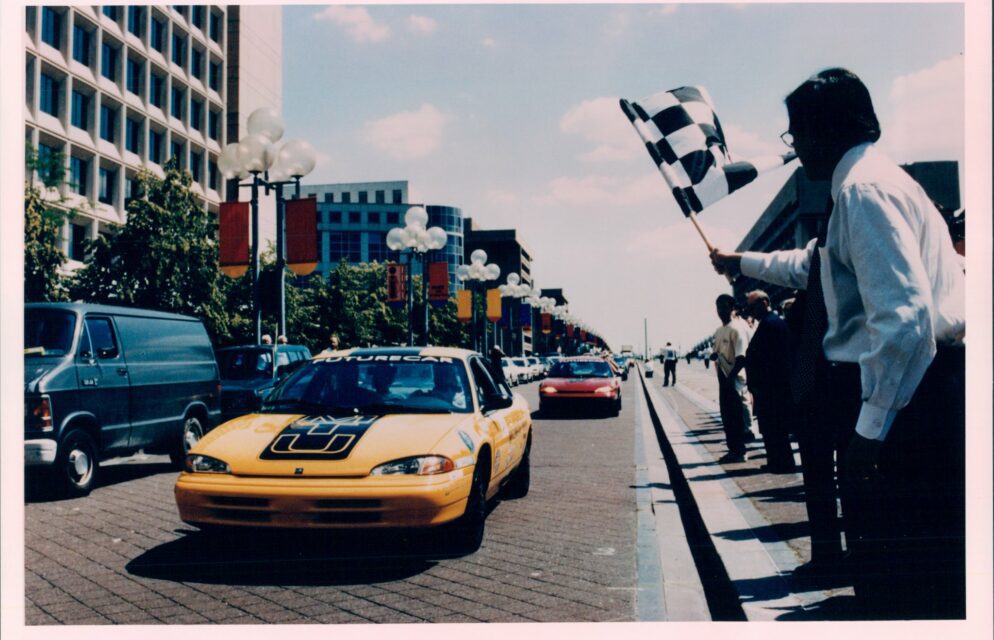
FutureCar
Inovations & Hightlights
FutureCar Challenge was a unique competition in which teams used advanced control strategies and hybrid electric vehicle powertrains to incorporate small engine technology and efficient electric motors. The competition was successful because of the support from the Partnership for a New Generation of vehicle (PNGV).
PGNV was formed by former President Clinton, former Vice President Al Gore, and the CEOs of Chrysler, Ford, and General Motors. This government and industry partnership included research support from scientists and engineers at universities, automotive suppliers, and small businesses. The main goals were to improve competitiveness in manufacturing; apply commercially viable innovation to conventional vehicles; and develop technologies for vehicles to achieve more than 80 miles per gallon while maintaining performance, safety, and affordability.
Together with PGNV, students were able to develop sustainable and advanced vehicle technologies during the four-year competition.
- Ten of the 12 vehicles were hybrid electric vehicle designs, including six parallel HEVs and four series HEVs.
- Six vehicles increased fuel economy in just the first year of FutureCar, despite weighing more than the stock vehicle.
- Both Concordia University and University of Wisconsin used dimethyl ether(DME) as their fuel selection in the 1998-1999 FutureCar Challenge.
- Ohio State University had an acceleration time of 11.17 seconds during the 1996 competition finale.
- University of California Davis, designed a plug-in hybrid electric vehicle that averaged 62 MPG in 1996
- In 1998, Lawrence Tech and University of Wisconsin-Madison demonstrated on-road fuel efficiencies above 70 miles per gallon gasoline equivalent (mpgge).
- Virginia Tech’s fuel economy in 1996 was 44.71 mpgge.
- Concordia University develop an electronic solenoid driving circuit to open the injector needle of their DME-fueled vehicle.
- Five vehicles met Federal Tier 0 standards, including five diesel hybrids and one ethanol hybrid in 1998.
- Virginia Tech and Texas Tech received fuel cell stacks to implement into their vehicle. Virginia Tech successfully ran as a fuel cell in 1999 and was one of the first groups to demonstrate this in the United States.
- The endurance event involved two 30-mile laps on Dearborn city streets. Five teams, including Concordia, West Virginia, Lawrence Tech, Wisconsin, and Ohio State, received the maximum score for this event by completing the distance in the allotted time.
- In 1999, the University of Wisconsin-Madison demonstrated that lightweight materials, performance, and fuel efficiency improvements can make significant progress to meeting PNGV goals when properly combined.
- In 1997, University of California – Davis demonstrated that aerodynamic improvements and a charge-depleting strategy could work.
Universities Involved
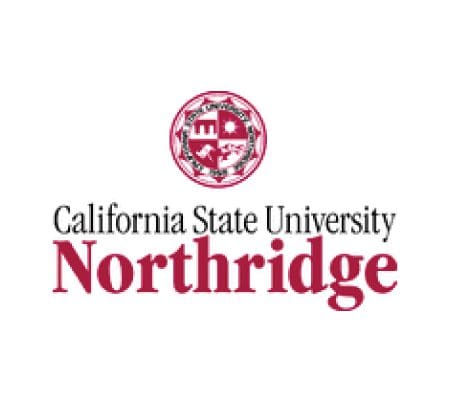
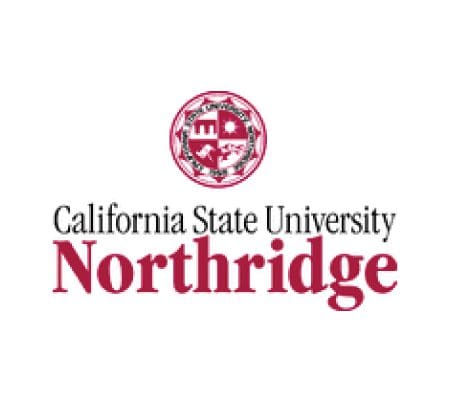
California State University, Northridge
Location
Northridge, CaliforniaFaculty Advisors
- Dr. Tim Fox
- Dr. Ben Mallard
- Dr. Gerald Davis
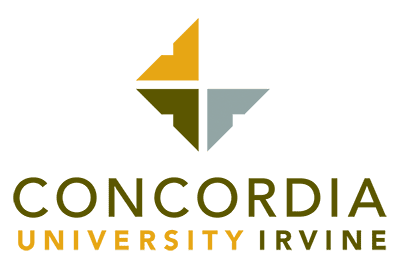
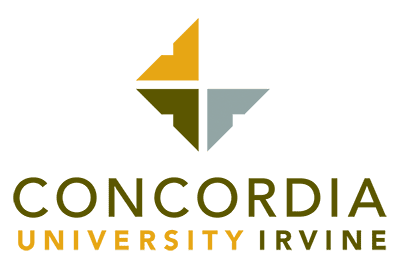
Concordia University
Location
St. Paul, MinnesotaFaculty Advisors
- Dr. Henry Hong
- Dr. T Krepec
- Dr. Mark VanVliet
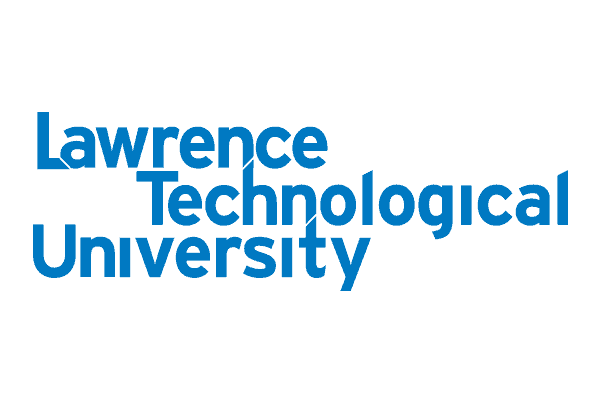
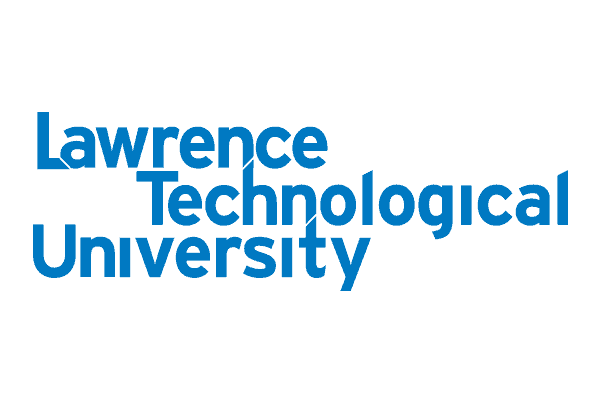
Lawrence Technological University
Location
Southfield, MIFaculty Advisors
- Dr. Greg Davis
- Dr. Rick Johnston
- Ken Haubert
- Jim Swan
- Mike Taila
- Craig Hoff
- Nick Brancik
- Dr. Richard Stanley
- Dr. Robert Farrah
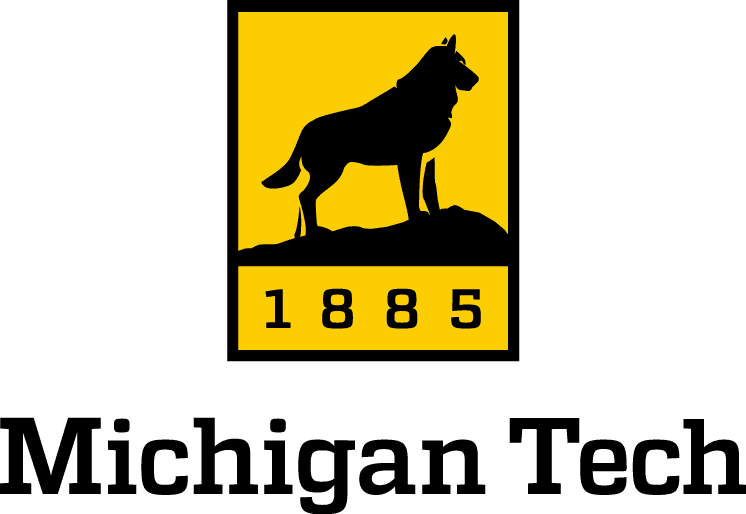
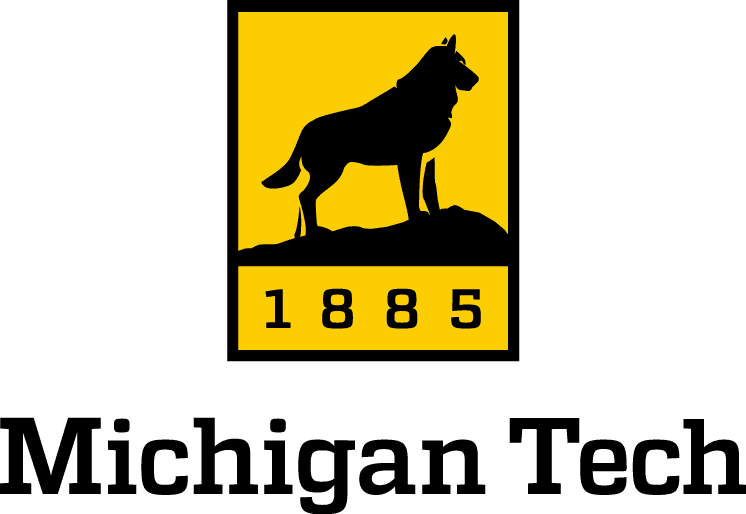
Michigan Technological University
Location
Houghton, MichiganFaculty Advisors
- Dr. Carl Anderson
- Dr. Eric Baumgartner and
- Dr. John Beard
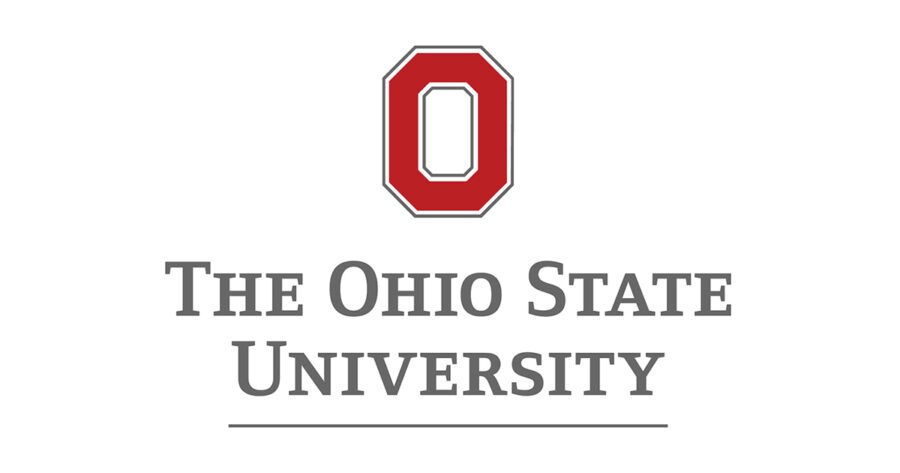
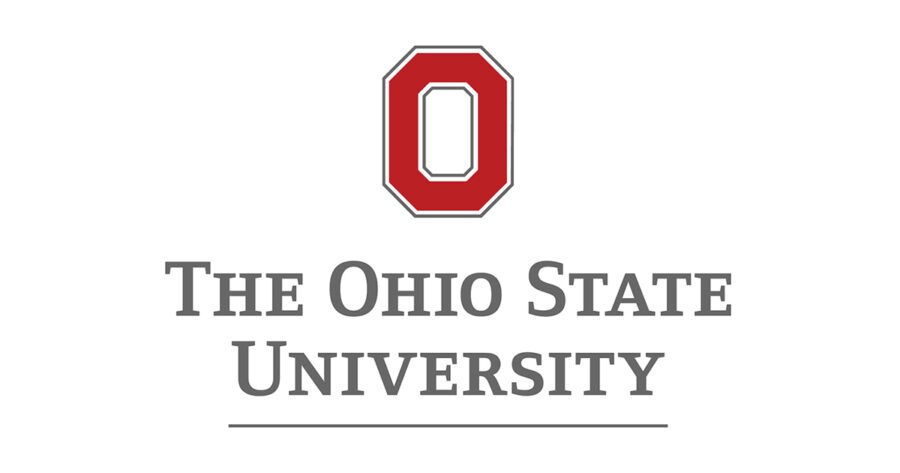
Ohio State University
Location
Columbus, OhioFaculty Advisors
- David Erb
- Ali Keynam
- Yan Guezennec
- Giorgio Rizzoni
- Gregory Washington
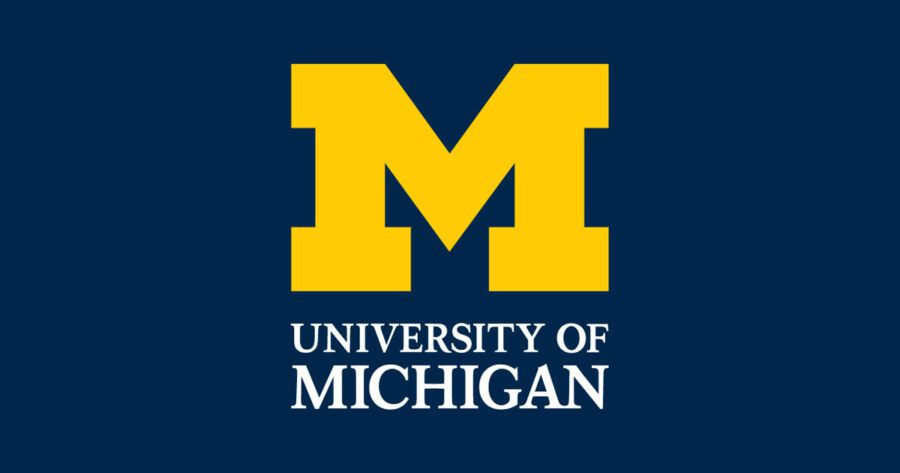
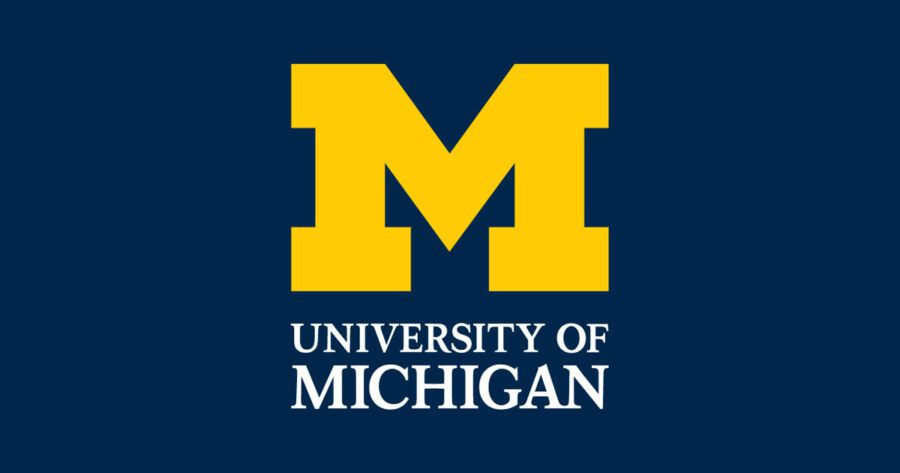
University of Michigan, Ann Arbor
Location
Ann Arbor, MichiganFaculty Advisors
- Dr. Tom Gillespie
- Ann Marie Sastry
- Mehrdad Haghi
- Valdis Liepa
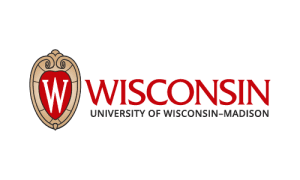
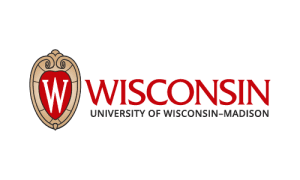
University of Wisconsin, Madison
Location
Madison, WisconsinFaculty Advisors
- Dr. Glenn Bower
- Wayne Milestone
- James Skiles
Winners & Awards
Each year, university teams compete in a variety of static and dynamic events that range from oral presentations to on-road vehicle testing to communications and business tactics. These static and dynamic events are judged by industry sponsors and professionals, both throughout the year and in-person at the year-end competition.
Year One 1995-1996
- 1st Place – Virginia Tech
- 2nd Place- Lawrence Technological University
- 3rd Place – University of Wisconsin-Madison
- 4th Place – Ohio State University
- 5th Place – Concordia University
- 6th Place – West Virginia University
- Most Energy Efficient Vehicle – Virginia Tech
- Best Acceleration – Ohio State University
- Best Dynamic Performance – Ohio State University
- Best Over-the-Road Range – University of Wisconsin-Madison
- Lowest Emissions – Virginia Tech
- Best Technical Report- University of California, Davis
- Best Engineering Design – Lawrence Technological University
- Best Overall Dynamic Performance – Virginia Tech
- Best Consumer Acceptability – Concordia University
- Best Application of Advanced Technology – Lawrence Technological University
- Manufacturing and Cost Special Award – University of Illinois at Chicago
- Lowest Vehicle Driving Losses- Ohio State University
- Best Safety – University of Maryland
- Best Application of Advanced Materials- Lawrence Technological University
- Best Use of Alternative Fuels – Virginia Tech
- Best Workmanship – Virginia Tech
- Best Teamwork- University of California, Davis
- Sportsmanship- University of Wisconsin-Madison
- Spirit of the Challenge – University of Maryland
- Best Skit- University of Illinois at Chicago
Year Two 1996-1997
- 1st Place: Virginia Tech
- 2nd Place: Ohio State University
- 3rd Place: Lawrence Tech
- 4th Place: University of Wisconsin-Madison
- 5th Place: Concordia University
- 6th Place: West Virginia University
- Most Energy Efficient Vehicle: Virginia Tech
- Best Engineering Design: Lawrence Tech
- Best Acceleration: Ohio State University
- Lowest Emissions: Virginia Tech
- Best Consumer Acceptability: Concordia University
- Best Dynamic Performance – Virginia Tech
- Best Over-the-Road Range – University of Wisconsin-Madison
- Lowest Emissions – Virginia Tech
- Best Technical Report- University of California, Davis
- Best Overall Dynamic Performance – Virginia Tech
- Best Application of Advanced Technologies: Lawrence Tech
- Manufacturing and Cost Award: University of Illinois at Chicago
- Best Safety: University of Maryland
- Best Use of Alternative Fuels: Virginia Tech
- Lowest Vehicle Driving Losses- Ohio State University
- Best Use of Alternative Fuels – Virginia Tech
- Best Workmanship – Virginia Tech
- Best Teamwork- University of California, Davis
- Sportsmanship- University of Wisconsin-Madison
- Spirit of the Challenge – University of Maryland
- Best Skit- University of Illinois at Chicago
Year Three 1997-1998
- 1st Place (tie): Virginia Tech & University of Wisconsin-Madison
- 3rd Place: Lawrence Tech
- 4th Place: Michigan Tech
- 5th Place: University of Maryland
- 6th Place: Concordia University
- Most Energy Efficient Vehicle: Ohio State
- Best Engineering Design: Virginia Tech
- Best Acceleration: Virginia Tech
- Best Dynamic Handling: Virginia Tech
- Best Endurance (tie): Lawrence Tech and University of Wisconsin-Madison
- Lowest Emissions: University of Maryland
- Best Technical Report: University of Maryland
- Best Vehicle Design: Virginia Tech
- Best Oral Design Presentation: Lawrence Tech
- Best Consumer Acceptability: Virginia Tech
- Best Appearance: University of Illinois at Urbana-Champaign
- Lowest Vehicle Driving Losses – University of Wisconsin-Madison
- Best Safety: Texas Tech
- Best Use of Alternative Fuels: University of Maryland
- Best Used of Advanced Materials: University of Wisconsin-Madison
- Innovation in Aluminum: University of Wisconsin-Madison
- Best Workmanship: University of Illinois at Urbana-Champaign
- Best Teamwork: University of Wisconsin-Madison
- Sportsmanship Award: Michigan Tech
- Spirit of the Challenge: Texas Tech
- Best Solo: Virginia Tech
- Outstanding Faculty Advisor – Dr. Andy Frank, UC Davis
Year Four 1998-1999
- 1st Place – University of Wisconsin, Madison
- 2nd Place – Virginia Tech
- 3rd Place – Michigan Technological University
- 4th Place – University of Maryland
- 5th Place – Ohio State University
- 6th Place – Lawrence Technological University
- Most Energy Efficient Vehicle – University of Wisconsin, Madison
- Best Acceleration – University of Wisconsin, Madison
- Best Dynamic Handling- University of Wisconsin, Madison
- Best Over-the-Road Fuel Efficiency – University of Wisconsin, Madison
- Lowest Emissions – Virginia Tech
- Best Technical Report – University of California, Davis
- Best Vehicle Design Inspection – University of California, Davis
- Best Oral Design Presentation – Virginia Tech
- Best Consumer Acceptability – Michigan Technological University
- Best Use of Advanced Technologies – University of California, Davis
- Best Appearing Vehicle- University of Wisconsin, Madison
- Innovations in Aluminum – University of Wisconsin, Madison
- Best Use of Alternative Fuels – University of Maryland
- Best Workmanship – University of Wisconsin, Madison
- Best Teamwork – Virginia Tech
- Sportsmanship- Michigan Technological University
- Spirit of the Challenge – Concordia University
- Best Skit – Concordia University
- Best Handling FutureCar – University of Wisconsin, Madison
- Outstanding Faculty Advisor – Dr. Doug Nelson, Virginia Tech
Sponsors
Below are the list of sponsors who helped make FutureCar possible:
FutureCar Media Coverage
Select a tab above to view content
- FutureCar Media Report
- DOE, USCAR Sponsor Student Competition to Build “Future Car” – Fall 1995
- Universities To Develop Car of the Future – October 5, 1995
- Virginia Tech Ranks First at Mid-Way Mark of FutureCar Challenge – Summer/Fall 1996
- Students gear up for phase one of FutureCar Challenge – June 25, 1996
- Engineering students compete in FutureCar Challenge – June 1996
- COE’s Team Paradigm challenged to build FutureCar – Fall 1996
- Highway To a High-Mileage Future
- Unique Mobility Drive System Powers UC Davis Win at 1997 FutureCar Challenge – June 18, 1997
- Virginia Tech Students Receive $250,000 Fuel Cell From DOE For The 1998-99 Futurecar Challenge – December 3, 1997
- 1998 FutureCar Challenge – August 1, 1998
- Students change the future – August 22, 1998
- Rockefeller Welcomes WVU Students “Future” Car to Washington – June 10, 1999
- For Second Straight Year: First Place Winner – University of Wisconsin Wins Innovations in Aluminum Award at FutureCar Challenge. – June 11, 1999
- Not Just for Soft Drink Cans Anymore – June 14, 1999
- 1999 FutureCar Challenge – July 1, 1999
- 1996 Info Sheet
- 1996 Program
- 1997 Program
- 1997 Results
- 1998 Info Sheet
- 1998 Program
- 1998 Results
- 1999 Info Sheet
- 1999 Program
- FutureDrive Newsletter – Summer 1995
- FutureDrive Newsletter – Winter 1995/1996
- FutureDrive Newsletter – Spring 1996
- FutureDrive Newsletter – Summer/Fall 1996
- FutureDrive Newsletter – Winter 1996/1997
- FutureDrive Newsletter – Spring 1997
- FutureDrive Newsletter – Summer/Fall 1997
- FutureDrive Newsletter – Spring 1998
- FutureDrive Newsletter – Summer 1998
- FutureDrive Newsletter – Winter 1998
- FutureDrive Newsletter – Spring 1999
- FutureDrive Newsletter – Summer 1999
- FutureDrive Newsletter – Fall 1999
- FutureDrive Newsletter – Winter 1999
- The Design and Development of the University of California, Davis FutureCar – February 1997
- Energy Consumption Study for a Hybrid Electric Vehicle – February 24, 1997
- Investigation of Practical HEV Test Procedures with Prototypes from the 1997 FutureCar Challenge – February 23, 1998
- Design of a Charge Regulating, Parallel Hybrid Electric FutureCar – February 23, 1998
- Intelligent Control of Hybrid Vehicles Using Neural Networks and Fuzzy Logic – February 23, 1998
- Development and Testing of a Second Generation ULEV Series HEV at West Virginia University – February 23, 1998
- Validation of ADVISOR as a Simulation Tool for a Series Hybrid Electric Vehicle – February 23, 1998
- Nickel-Metal Hydride Batteries For ZEV-Range Hybrid Electric Vehicles
- Texas Tech University Develops Fuel Cell Powered Hybrid Electric Vehicle for FutureCar Challenge 1998 – March 1, 1999
- Simulation-Based Hybrid-Electric Vehicle Design Search – March 1, 1999
- Optimizing the University of Wisconsin’s Parallel Hybrid-Electric Aluminum Intensive Vehicle – March 6, 2000
- Integration of Fuel Cell Technology into a Hybrid Electric Vehicle – March 6, 2000
- Modeling and Validation of a Fuel Cell Hybrid Vehicle – April 2, 2000